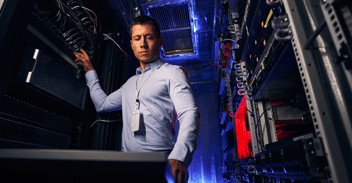
Gartner ha incluso il Digital Twin tra le cinque tendenze emergenti che guideranno l’innovazione tecnologica per il prossimo decennio. In effetti, consentendo alle Smart Factory la possibilità di sviluppare nuove opportunità di business, il Digital Twin, o “gemello digitale”, è già uno degli elementi fondamentali dell’Industria 4.0 ed è destinato a svolgere un ruolo strategico anche nella transizione in atto verso un’idea di fabbrica sempre più intelligente, sostenibile e resiliente propria del modello Industry 5.0, al centro del quale non c’è soltanto efficienza e produttività, ma anche un approccio human centric.
Una recente ricerca di Straits Research rivela che il mercato dei Digital Twin nel mondo è in continua crescita: dai 9,7 miliardi di dollari del 2022, si prevede raggiungerà i 185 miliardi di dollari entro il 2031, crescendo a un CAGR (Compounded Average Growth Rate) del 38,8% durante nel periodo 2023–2031. La quota di mercato più alta spetta al segmento automobilistico e dei trasporti, che si stima avrà un CAGR del 39,2% durante il periodo di previsione, ma sono tanti altri i settori in cui i Digital Twin trovano applicazione, dall’energia all’aerospazio, dalle infrastrutture alle smart city fino al retail. Sono, infatti, molti i vantaggi offerti dalla simulazione in 3D e dalla prototipazione in termini di aumento della produttività, miglioramento della qualità del prodotto finale e riduzione dei tempi e costi di sviluppo, nonché dalla capacità di rivoluzionare e innovare il modo di monitorare e pianificare i processi produttivi.
In Italia, un utilizzo sistemico dei Digital Twin nel settore manufatturiero, genererebbe un incremento delle produttività del +4,5% rispetto allo scenario attuale, contribuendo al PIL con 12 miliardi di euro (+0,7%), il valore dell’intera filiera tessile italiana o del comparto aeronautico e aerospaziale, con un impatto travolgente a livello di produttività, sostenibilità e innovazione. A rivelarlo lo studio “Digital Twins for the Twin Transitions”, realizzato da Atos Italia in partnership con The European House – Ambrosetti, secondo il quale, come conseguenza dell’adozione, si avrebbe anche un taglio dei costi della bolletta energetica tra il 16 e il 33%, un accorciamento del time to market di -35%, nonché un contributo in termini di sostenibilità che porterebbe a una diminuzione delle emissioni di gas serra di 30,4 milioni di tonnellate di CO2, il 23% di quelle che l’Italia si è impegnata ad abbattere entro il 2030 nell’ambito della strategia UE.
Cos’è il Digital Twin?
Con Digital Twin, secondo quanto riportato nello studio Ambrosetti, si intende una “copia digitale interattiva di un oggetto o un sistema complesso, che permette di analizzarne, simularne e predirne il comportamento”. I Digital Twin, quindi, sono repliche virtuali interconnesse di sistemi fisici, in cui il continuo scambio tra oggetto digitale e reale della grande mole di dati acquisiti dai sensori posti sul sistema reale, grazie algoritmi di Intelligenza Artificiale (AI) e Machine Learning (ML), consente di replicarne in tempo reale il comportamento e predire e ottimizzare il suo funzionamento.
La tecnologia del Digital Twin è abilitata dall’adozione convergente di quattro tecnologie, Internet of Things, Intelligenza Artificiale, Big Data, High Performance Computing (HPC), nelle quali i dati vengono scambiati grazie ad una connettività iper-veloce, necessaria per l’elaborazione in tempo reale dei Big Data e resi fruibili grazie a sistemi di User Experience Design (UX Design), che assicurano un facile utilizzo per l’utente finale.
L’insieme di queste tecnologie consente di definire le caratteristiche di un Digital Twin,che, secondo il rapporto Ambrosetti, è:
- Multifisico, perché coinvolge o simula più sistemi o fenomeni fisici;
- Multiscala, in quanto capace di riprodurre il comportamento di un singolo componente, dell’impianto o dell’intera smart factory, sia alla scala macro, che micro.
- Modellabile, sulla base delle parti e dei componenti che compongono il sistema;
- Multidisciplinare, perché fa leva sull’integrazione di diversi ambiti disciplinari, tra cui l’ingegneria, l’informatica, la fisica, la chimica e la matematica;
- Probabilistico, in quanto utilizza metodi statistici e algoritmi di machine learning per le simulazioni del sistema reale a fini predittivi;
- Dinamico, perché costantemente aggiornato, nell’ottica di un miglioramento continuo.
I vantaggi del Digital Twin per la Smart Factory
Grazie alle sue caratteristiche e alla capacità di restituire una “fotografia” aggiornata in tempo reale dello stato dell’asset fisico, sia esso un prodotto, un sistema, un processo o un servizio, il Digital Twin consente di rivoluzionarne l’intero ciclo di vita. A partire dalla fase di design, attraverso un’attività sperimentale con la quale prototipare nuove idee e ipotizzare virtualmente scenari “what if” con i quali ridurre i costi di sviluppo e migliorare l’affidabilità dell’asset, a quella di una produzione testata e ottimizzata, in cui questa tecnologia consente un costante miglioramento della qualità di un prodotto.
Da quella di funzionamento e vita operativa, con la possibilità di attivare un’assistenza per i clienti e ricevere dati sulle prestazioni e le condizioni operative per generare approfondimenti relativi alle tendenze di utilizzo, comprendendo meglio le esigenze specifiche del cliente e apportare miglioramenti a prodotti, operazioni e servizi esistenti e fornendo le linee guida dell’innovazione, alla fase manutentiva, che consente di abbattere i costi, prevedere in anticipo comportamenti anomali, ridurre rischi, tempi di inattività, inefficienze ed errori e aumentare la competitività dell’azienda, sviluppando nuove opportunità e pianificando i business futuri mediante appropriate simulazioni basate su AI e ML.
Il Digital Twin consente, inoltre, di efficientare anche la fase di smaltimento e fine vita del prodotto, fornendo indicazioni utili per decidere quale componente riutilizzare, ricondizionare, riciclare o rottamare.
Digital Twin e Intelligenza Artificiale: cosa ci aspetta?
Grazie agli sviluppi dell’AI e dell’apprendimento automatico, tramite il quale il sistema impara dall’esperienza, nel corso degli anni, quindi il Digital Twin si è evoluto da simulatore, a sistema ibrido in grado di svolgere ragionamenti induttivi, sulla base dei quali prevedere in modo accurato il comportamento di un determinato indicatore e replicare contesti più vasti, come un intero shopfloor, con tempi ridotti e meno spese.
In un’ottica Industry 5.0 e in accordo con l’approccio “Human Centric”, in un prossimo futuro, la raccolta dati potrà essere effettuata anche tramite dispositivi e sensori portatili con i quali rendere l’ambiente migliore e più sicuro per il lavoratore, in un contesto in cui la cooperazione uomo-macchina porti a risultati di efficienza e di resilienza dell’azienda.
Abbracciando il concetto di sostenibilità, l’adozione delle tecnologie Digital Twin permetterà un uso ancora più efficiente delle risorse, riducendo gli sprechi, quantificando l’impatto ambientale della produzione e confrontando diversi scenari, sulla base dei quali controllare i consumi energetici, ridurre la quantità di rifiuti, suggerire l’uso di materiali riciclabili nel ciclo di produzione, aiutando le aziende a diventare sempre più sostenibili, oltre che smart.